Gypsum powder is one of the five major gel materials, which is processed through crushing, grinding and other processes. It is widely used in construction, building materials, industrial molds and art models, chemical industry and agriculture, food processing, medicine and beauty and other applications. It is an important industrial raw material.
Gypsum has good sound insulation, thermal insulation, and fire resistance characteristics. In China, natural gypsum reserves are abundant and have been used for a long time. With the improvement of economic and technological levels, gypsum powder production equipment and processes also have more choices and more scientific configuration plans.
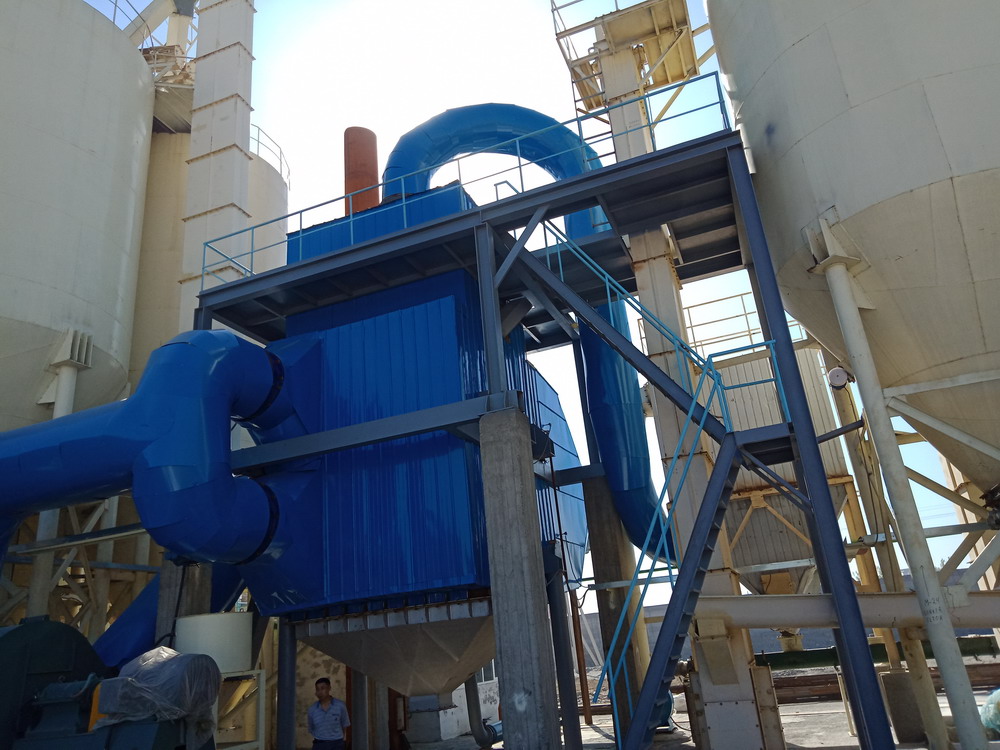
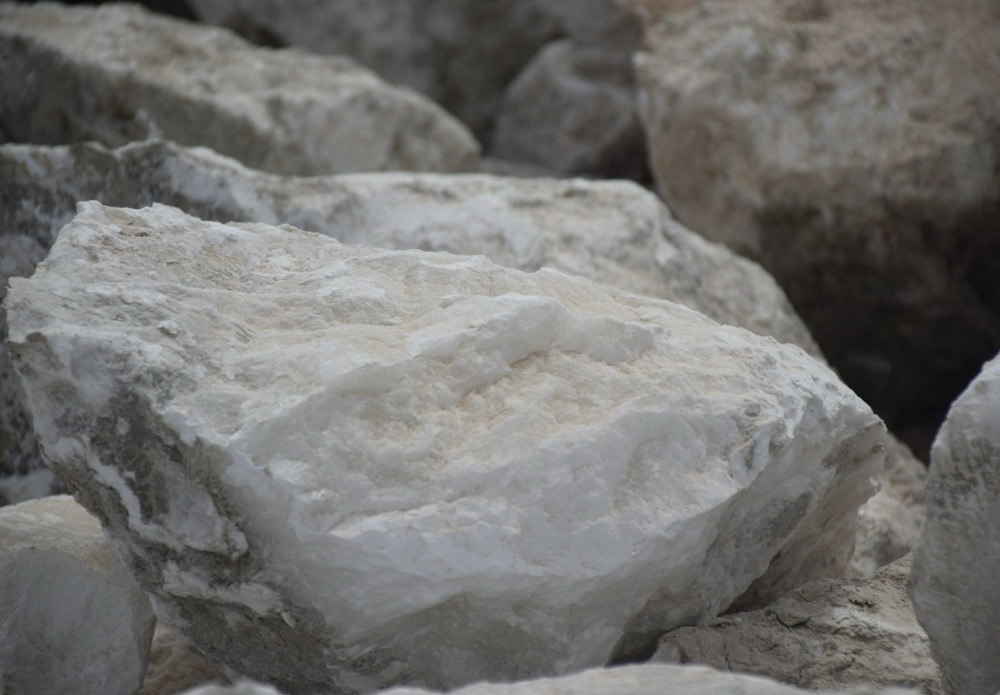
White and colorless transparent crystals are usually referred to as transparent gypsum, and sometimes they become gray, light yellow, light brown, and other colors due to impurities.
STEP1. crushing system
The size and specifications of gypsum ores are different after mining, and the applicable crushing equipment is selected for preliminary crushing treatment according to the actual situation, and the particles with particle size not greater than 35mm are broken.
STEP2. storage conveying system
The crushed gypsum raw material is transported to the storage bin by the elevator. The storage bin is designed according to the requirements of the material storage time to ensure the stable supply of materials. At the same time, all parts of the material turnover are using lifts to reduce the floor area.
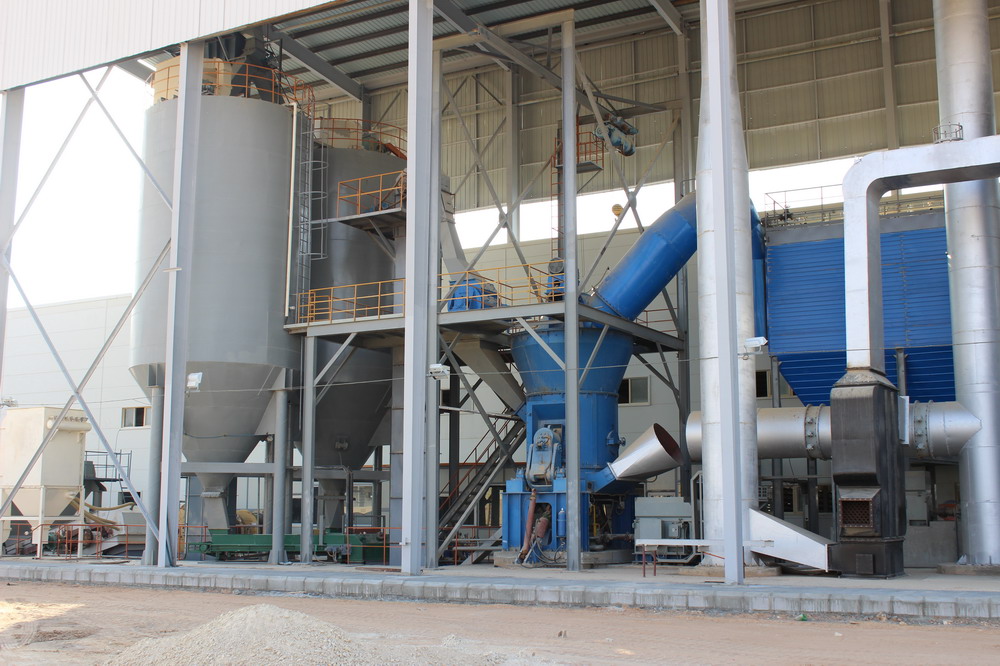
STEP3. grinding system
— The grinding process is the core process of gypsum powder production. The gypsum raw material in the storage bin enters the grinding machine through the vibration feeder for finishing. The electromagnetic vibration feeder is set under the storage bin, which is interlocked with the mill to adjust the supply of materials in time according to the running condition of the mill.
— The material is uniformly and continuously fed into the mill by the electromagnetic vibration feeder for grinding.
— The pulverized gypsum powder is blown out by the air flow from the mill blower and graded by the analytical machine above the main engine. The powder with the fineness meeting the specifications enters the large cyclone collector with the air flow, and is discharged as the finished product through the powder outlet pipe after collection.
— The finished product falls into the screw conveyor and is transported to the next system for calcining. The air flow flows from the return duct of the cyclone collector into the blower. The whole air path system is closed circulation and flows under negative pressure. Due to the water contained in the ground raw materials and the evaporation into gas during the grinding process, resulting in an increase in the air volume in the circulating air path, the increased air volume is introduced from the pipe between the large cyclone collector and the blower to the bag dust collector, and then discharged into the environment to ensure that the environment is clean.
— The particle size of the material through the grinding system is changed from 0-30mm to 80-120 mesh, which meets the requirements of the fineness of gypsum powder.
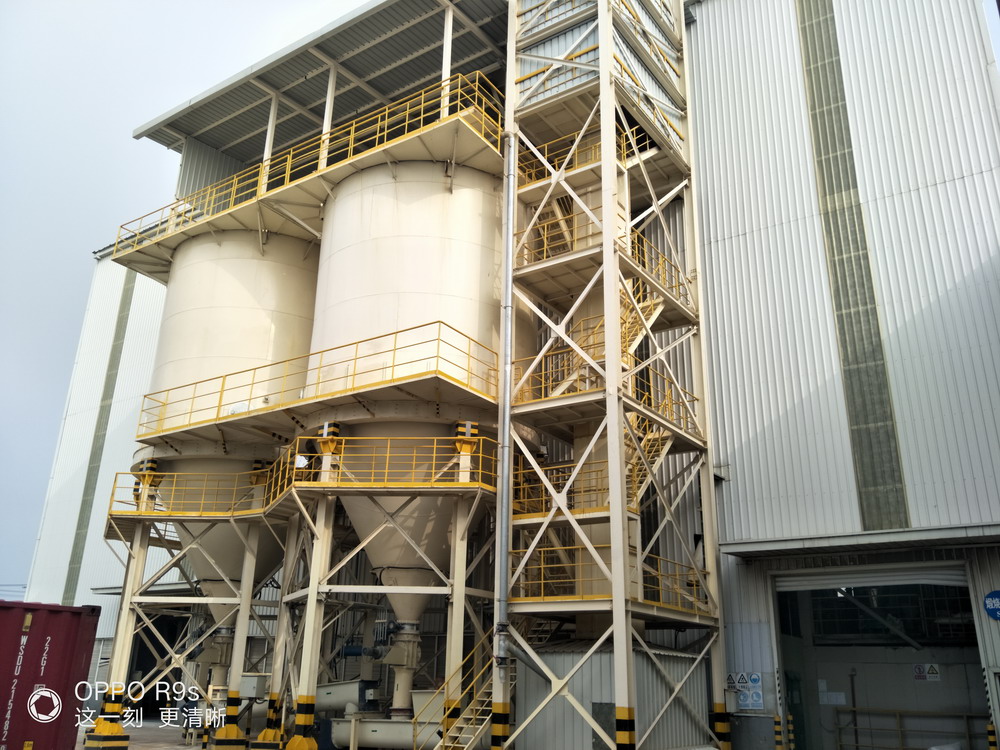
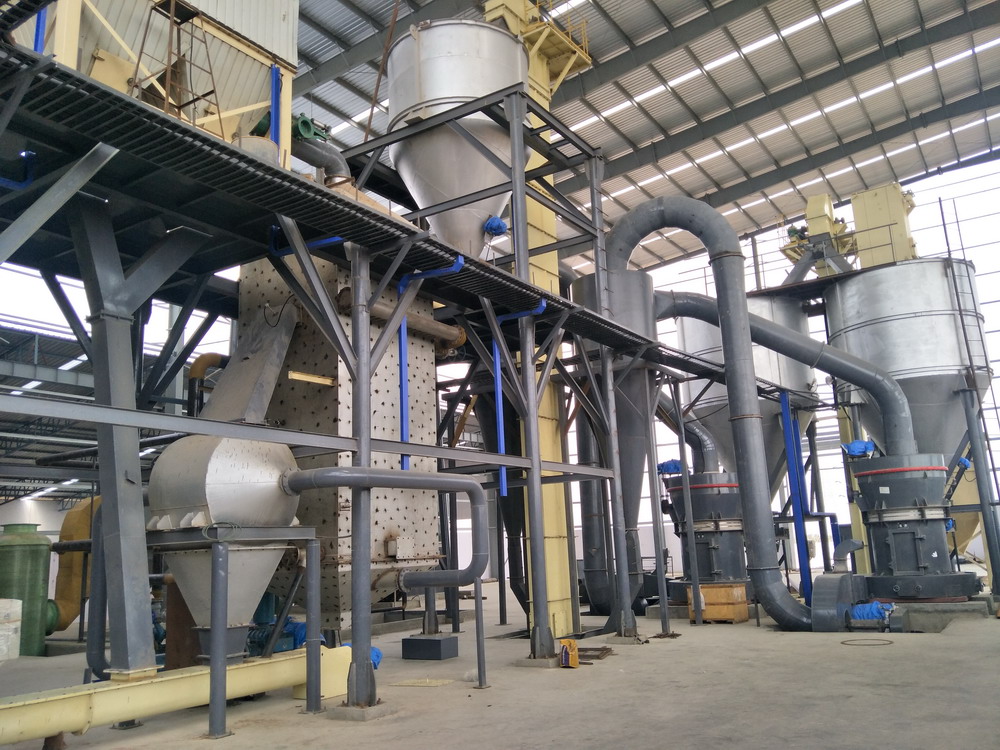
STEP4. calcining system
After grinding is completed, the pulverized gypsum powder is sent to the rotary kiln for calcining by the powder separator, the plaster of Paris is sent to the storage storage by the elevator, and the materials that do not meet the requirements are continued to be returned to the mill for grinding; The system mainly includes lifting machine, boiling furnace, electrostatic dust removal, Roots fan and other equipment.
STEP5. electrical control system
The electrical control system adopts the current advanced centralized control, DCS control or PLC control, and the control components are selected internationally well-known brand products
Setting up a gypsum powder production line requires careful planning and a good understanding of the overall process.
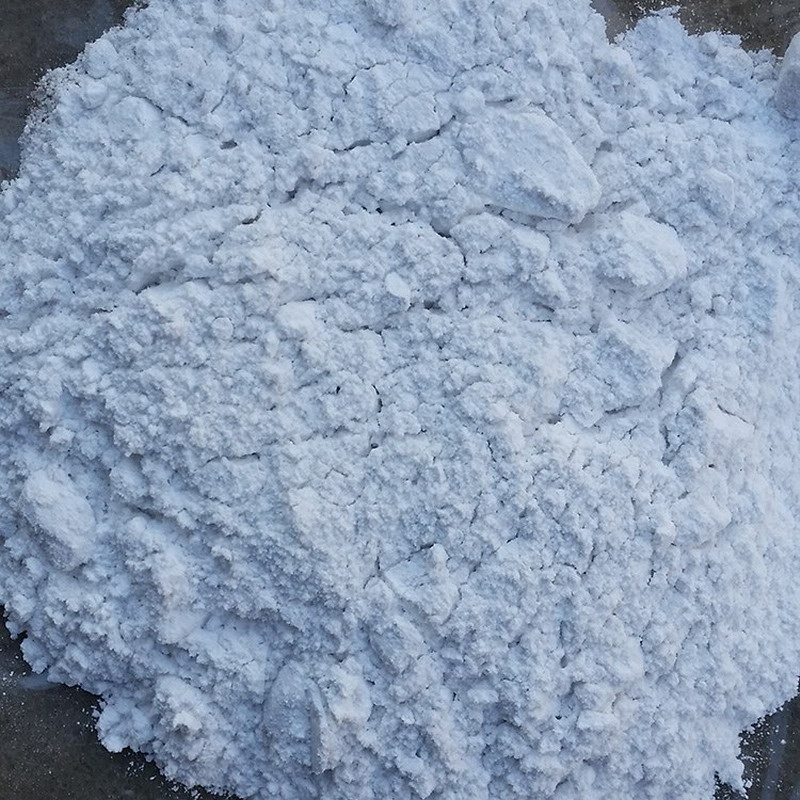
How To Set Up a Gypsum Powder Production Line From Scratch
Gypsum powder is widely used in the construction industry for making drywall, plaster, and other building materials. Here are the key steps and considerations you need to be aware of when setting up a gypsum powder production line:
Market Research:
Start by conducting thorough market research to understand the demand for gypsum powder in your region. Identify potential customers and competitors.
Business Plan:
Develop a comprehensive business plan that outlines your goals, budget, and production capacity. Include financial projections and a timeline for breaking even and generating profits.
Location and Facilities:
Select a suitable location for your production facility, considering factors like proximity to gypsum mines or sources, transportation infrastructure, and availability of utilities such as water and electricity.
Raw Materials:
Gypsum is the primary raw material for producing gypsum powder. Ensure a reliable source of gypsum supply, either through direct ownership of gypsum mines or through contracts with gypsum suppliers.
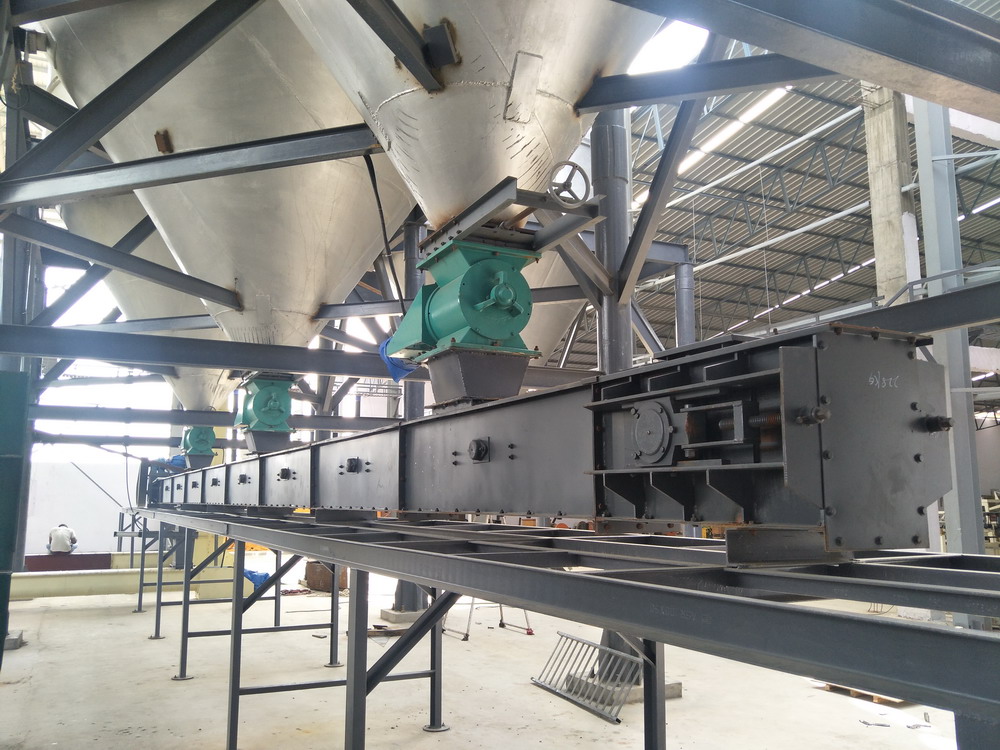
Equipment and Machinery:
Acquire the necessary equipment and machinery for gypsum powder production, including crushers, mills, calciners, and packaging machines. The specific equipment may vary depending on the production process you choose.
Production Process:
There are different methods for producing gypsum powder, including the calcination process, wet processing, or a combination of both. Choose the most suitable production process based on the quality and quantity of gypsum powder you intend to produce.
Quality Control
Implement quality control measures to ensure that the gypsum powder meets industry standards and customer expectations. This may include testing for particle size, purity, and moisture content.
Environmental Compliance:
Be aware of environmental regulations and ensure that your production process complies with local, state, and national environmental standards. Gypsum production may generate waste that needs proper disposal.
Workforce:
Hire and train skilled personnel who are knowledgeable about the production process and quality control. Safety training is also essential to prevent accidents and injuries.
Packaging and Distribution:
Decide on the packaging options for your gypsum powder and establish distribution channels to reach your target customers, including wholesalers, retailers, and construction companies.
Marketing and Sales:
Develop a marketing strategy to promote your gypsum powder and build a customer base. Attend industry trade shows, create a website, and use digital and traditional marketing methods to reach potential buyers.
Financial Management:
Keep accurate financial records and manage your finances efficiently. Monitor costs, revenue, and profitability regularly.
Permits and Licensing:
Obtain the necessary permits and licenses to operate a gypsum powder production facility. This may involve local zoning permits, environmental permits, and business licenses.
Safety and Compliance:
Ensure that your production facility adheres to safety regulations and standards. Provide adequate safety equipment and training for your employees.
Sustainability:
Consider implementing sustainable practices in your production process, such as reusing waste materials or reducing energy consumption, to minimize your environmental footprint.
Setting up a gypsum powder production line can be a complex and capital-intensive venture, so it's important to conduct thorough research and seek expert advice as needed. You should also be prepared for challenges that may arise in the course of establishing and running your business.
What processing machines are available?
Several processing machines are used in gypsum powder production lines, and the specific machines you need may vary depending on the production process you choose. Here are some common machines and equipment used in gypsum powder production:
Crushing Equipment:
Jaw Crusher: Used to crush large gypsum chunks into smaller pieces.
Hammer Crusher: Suitable for secondary or fine crushing.
Grinding Equipment:
Raymond Mill: Used for grinding gypsum to a fine powder.
Ball Mill: Another option for grinding and producing fine gypsum powder.
Ultrafine Mill: Used to produce ultra-fine gypsum powder
Calcination Equipment:
Rotary Kiln: Used in the calcination process to remove water from gypsum and convert it into stucco (calcined gypsum).
Drying Equipment:
Fluidized Bed Dryer: Used to dry the calcined gypsum to the desired moisture level before further processing.
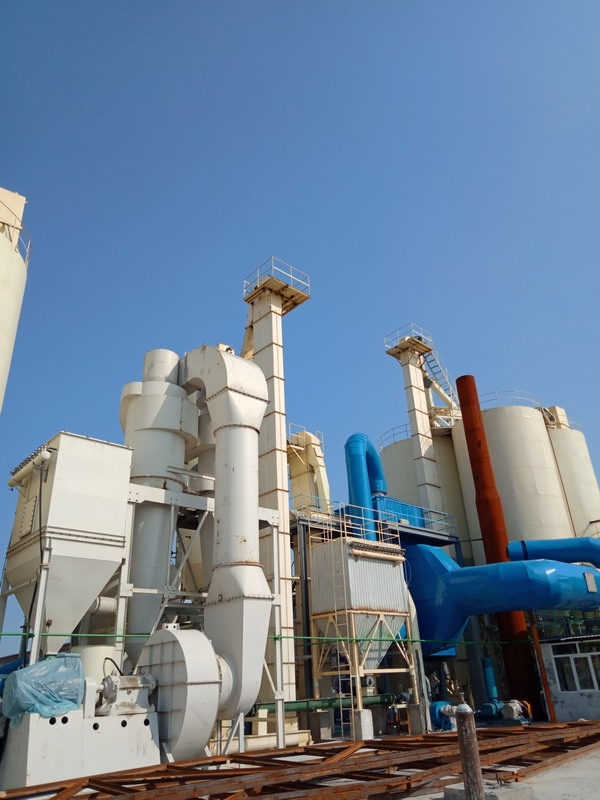
Conveying and Lifting Equipment:
Belt Conveyors: Transport raw materials and products between various processing stages.
Bucket Elevators: Used to lift and move materials vertically within the production line.
Mixing and Homogenizing Equipment:
Paddle Mixers: Used to mix additives and other materials with gypsum for uniform distribution.
Homogenizers: Ensure consistency of the gypsum mixture.
Material Handling Equipment:
Silos and Hoppers: Used for storing gypsum and other materials.
Screw Conveyors: Efficiently transport bulk materials.
Packaging Equipment:
Packaging Machines: Used to package the final gypsum powder into bags or containers for distribution.
Quality Control and Testing Equipment:
Sieves and Screens: Used to test and control particle size.
Moisture Analyzers: Monitor and control moisture content in the final product.
X-ray Fluorescence (XRF) Analyzers: Assess gypsum purity and composition.
Environmental Control Equipment:
Dust Collectors: Capture and remove dust and particles generated during the production process to maintain air quality.
Emission Control Systems: Ensure compliance with environmental regulations.
Automation and Control Systems:
PLC (Programmable Logic Controller) Systems: Used to control and monitor various machines and processes.
SCADA (Supervisory Control and Data Acquisition) Systems: Provide centralized control and data collection.
Safety Equipment:
Personal Protective Equipment (PPE): Ensure the safety of workers with gear such as helmets, gloves, and safety goggles.
The specific machines you need will depend on the scale of your operation, the production process you choose, and the desired quality of your gypsum powder. It's essential to consult with experts and suppliers in the industry to select the most appropriate equipment for your specific production needs. Additionally, keep in mind that safety and environmental compliance are critical aspects of any gypsum powder production process.
Post time: Mar-28-2024